

Within this shape, wide channels enable the handling of large solid particles without clogging. This design struggles to generate high pressures due to the lack of side walls, but can accommodate large solids.
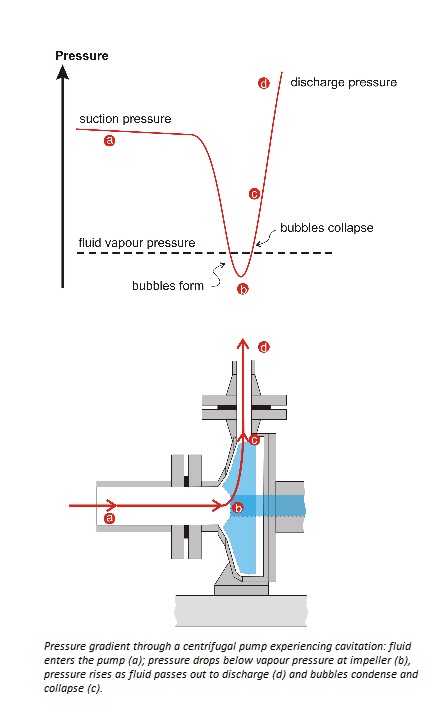
#CENTRIFUGAL IMPELLER DESIGN PRESSURE FREE#
It has a lower efficiency that other types due to its large free passage area. In this design only the vanes are visible enabling the unit to handle large solids, and remain easy to clean. Low shear by design, rotational speed is less than 1400rpm due to the impeller touching the casing.
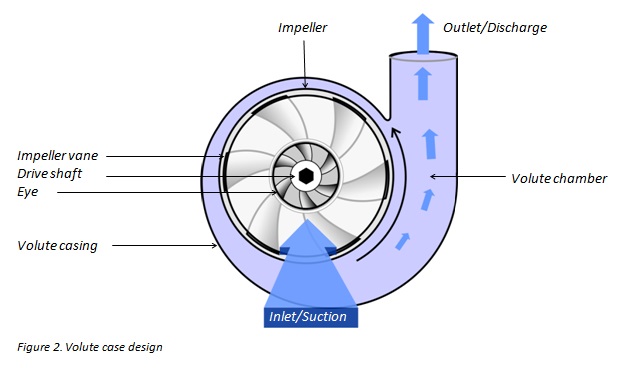
Designed to handle clean, viscous and solid laden liquids, solid particles fit between the blades meaning the unit can handle suspended solids such as fruit chunks up to 25mm in diameter. This design consists of curved rubber vanes which remain in contact with the pump casing enabling the unit to be self priming. This unit delivers the highest flow possible within a single casing. Typically used for clean liquids, without solids at high flows and relatively low heads with a double volute casing feeding both sides simultaneously. Used predominately in Split casing pumps, this design enables the pump to draw liquid through both sides of the impeller blade simultaneously. Double Suction (Split Casing and Double Suction Designs) The solid handling capability is defined by the space between the front and rear channels in the impeller which for small units could be measured in microns.įluid is drawn into the impeller eye (centre) before centrifugal forces direct fluid through blades, then directed towards the side of the pump casing, and expelled through the outlet. Typically, the closer that radial vanes are together, the tighter the tolerances and more enclosed impeller design, the higher the efficiency and lower the solid handling capacity due to limitations in free passage.īelow is a list of the 10 different types, their advantages and types of fluids they may be used with: Impeller types and flow pattern Closed or Enclosed (Centrifugal, Multistage and First Stage of Side Channel Pumps)ĭesigned for clean fluids with small particles, it is the design with the highest efficiency due to its tight clearances against the internal casing but also between impeller blades. There are 10 types of impeller each having different advantages and disadvantages depending on the application. Impeller types in Centrifugal Pumps vary in design depending on the fluid being handled, whether design is low or high pressure, and if the unit designed is self-priming or to handle entrained gas.Ĭare must be taken during selection to ensure a correct balance is achieved between desired outcome for the process and maintenance periods, whilst ensuring maximum process efficiency is obtained.
